Application-Specific Design For New Cat Wheel Material Handlers
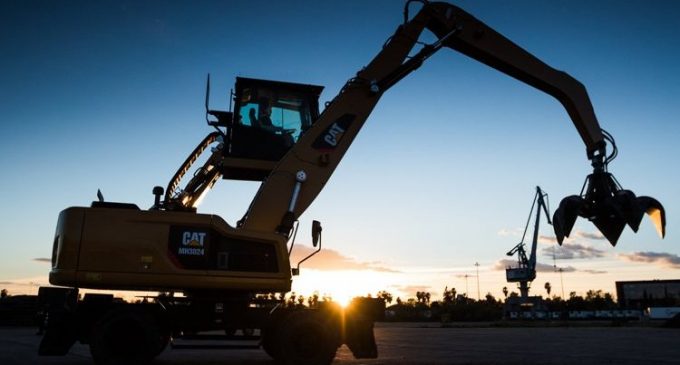
The new range of Cat® wheel material handlers (MH3022, MH3024, MH3026) maintains the Caterpillar purpose-built philosophy for these machines, while reflecting engineering refinements that tailor them more precisely to specific industrial applications. Further improvements for these 2018 models include features that support rapid return-on-investment and enhance overall performance, versatility, and safety.
The design of the new material handlers is focused on application efficiency and reduced owning costs. For example, users need not buy a machine with a wide undercarriage if materials being handled are low density, and shorter front linkages are available if the machine frequently works in confined spaces.
The MH3022, for instance, is an agile solution for handling jobs with space constraints, providing the necessary reach for tasks such as indoor sorting and waste-handling, yet providing application flexibility with a choice of two MH booms, three straight sticks with linkage, and two drop–nose sticks. The compact undercarriage is wide enough for excellent stability, while the centered position of the swing bearing allows equal capabilities when working over the front and rear.
If space-constraints are not an issue, the MH3024 is ideal for such tasks as waste handling, recycling, and bulk-material handling. The MH3024 features optimum reach with its long MH front linkage, and a choice of undercarriage configurations to meet all customer application needs. If the application is not stability-sensitive, then the new 2.75-m (9-ft.) undercarriage might be a perfect fit for the MH3024 working in typical conditions, as well as good fit for the MH3026 handling low density materials. In either instance, the machine’s footprint is adequate to ensure stability in normal operation, and, again, lifting capacities over the rear are increased by the symmetric position of the swing bearing
If work requires greater lifting capacities and a larger working envelope, then the MH3026 is the optimum machine, equipped with a long MH boom and providing a choice of three drop-nose sticks—ranging in length from 4.9 to 5.9 m (16.1 to 19.3 ft.), three straight sticks—and a choice of three undercarriage sizes.
The flexible design of the new material handlers also contributes to ease of transporting these machines—a sure way to better control costs. Two drop-nose sticks for the MH3022 and MH3026 are now available, having lengths of 4.5 m (14.75 ft.) and 5.5 m (18.1 ft.). The new sticks can be an efficient solution when moving a machine between jobsites is a frequent occurrence, allowing transport without removing the stick. Sticks are designed to keep transport heights below the critical 4-m (13.1-ft.) dimension for significant time/cost savings.
Another noticeable addition for the new models is the front push blade, now available for all undercarriage types. These blades provide an easy way to clear the working area and push materials commonly encountered in waste and mill-yard applications. Working on surfaces free of debris can further extend tire life, resulting in greater operational efficiency.
Operational efficiency gets a further boost with redesigned, optimized, Cat orange-peel grapples. Designed to be an exact match between tool and machine, the new grapples can contribute to decreased fuel consumption—by as much as 15 percent in some applications. The grapples feature reduced weight for shorter cycle times and increased productivity. Additional cost savings are available through the increased durability of the grapples, which have castings in place of welded structures in high stress areas.
Operator health and safety are primary design goals for the new material handlers. To that end, an Advanced Cab Filtration system, available as an integrated option from the factory, is recommended when machines work in dusty, contaminated environments, especially indoors. The system almost completely eliminates dust and contaminants (insecticides, spores, fungi, bacteria, or vapors—for example) from entering the cab. In addition, the system eliminates the need to add cumbersome after-market filtration systems to the machine. Also, an Easy Cab Access option, which installs steps on the front and rear of the undercarriage, facilitates cab ingress/egress when the upper frame is not aligned with the chassis.